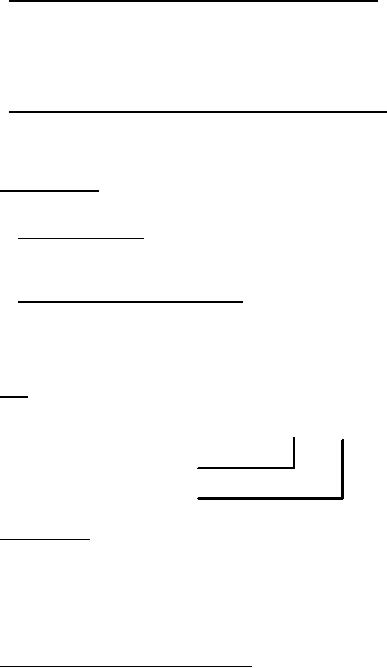
MIL-PRF-24794A
approval is presently appropriate for the pending contract. Unless
specifically requested to do so in the solicitation, bidders should not submit
alternate bids.
6.3.1 Test equipment and inspection facilities. Provisions for test and
measuring equipment and inspection facilities of sufficient accuracy, quality,
and quantity to permit performance of the required inspections must be the
responsibility of the contractor. The establishment and maintenance of a
calibration system to control the accuracy of the measuring and test equipment
must be in accordance with ANSI/NCSL Z540-1.
6.3.2 Alternate forms of conformance inspection. Requests for alternate
forms of quality conformance inspection (see 4.5) must be submitted to the
contracting officer. Alternate forms of quality conformance inspection may be
used upon written approval by the contracting officer.
6.4
Definitions.
Definitions of terms shall be in accordance with TIA/EIA-
440.
6.4.1 First contract. The first contract is considered to be the first
contract under which a manufacturers' material is supplied to any acquiring
activity under this specification.
6.4.2 First contract inspection. First contract inspections are
inspections required in addition to first article inspections for the first
contract in which this specification is invoked. First contract inspections
are intended to evaluate basic material properties that are primarily a
function of the product formulation, not the product manufacturing process.
6.5
PIN.
The PIN for this adhesive should contain the following:
M24794-1
Basic specification number
Basic product identifier
6.6 Shelf life. Products procured to this specification should not be used
for fiber optic termination purposes under any conditions if the date of
manufacture has passed by more than 36 months. If products procured to this
specification are exposed to temperatures higher or lower than the
temperatures specified in 3.5.1, the shelf life may be different than that
specified and the manufacturer should be contacted to determine the
appropriate shelf life under the actual storage conditions.
6.7 Material safety data sheets. The material covered by this
specification contains material(s) which may be hazardous to personnel and a
Material Safety Data Sheet (MSDS) is needed for employee safety programs.
Contracting officers will identify those activities requiring copies of
completed MSDS prepared in accordance with FED-STD-313. In order to obtain
the MSDS, FAR clause 52.223-3 must be in the contract.
10
For Parts Inquires call Parts Hangar, Inc (727) 493-0744
© Copyright 2015 Integrated Publishing, Inc.
A Service Disabled Veteran Owned Small Business